
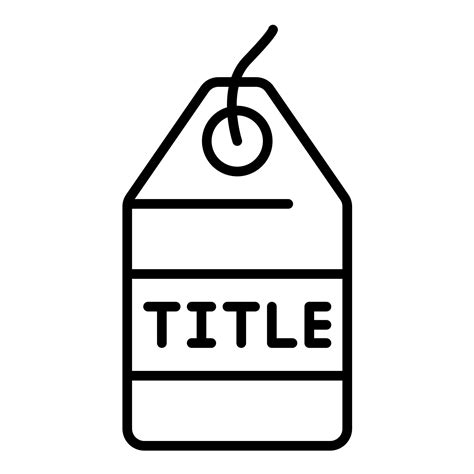
Creating miniature clay folks could be an extremely rewarding and pleasurable expertise. With just some easy supplies and just a little endurance, you may convey to life distinctive and charming characters that may add a private contact to your property décor or make considerate presents for family members. Whether or not you are a seasoned artist or an entire newbie, embarking on this artistic journey is certain to spark your creativeness and supply hours of enjoyment.
The method of crafting clay folks is surprisingly accessible. All you want is a couple of fundamental supplies, akin to polymer clay, sculpting instruments, and acrylic paint. Polymer clay is a flexible materials that is available in a variety of colours and textures, permitting you to customise your creations to fit your style. Sculpting instruments aid you form and refine your figures, whereas acrylic paint provides coloration and element to convey them to life.
The great thing about making clay folks lies within the limitless prospects it gives. From whimsical and cartoonish characters to practical and lifelike figures, the one restrict is your creativeness. Whether or not you select to create a miniature model of your self, a beloved pet, or a fantastical creature, the method is each difficult and rewarding. With every clay particular person you create, you may develop your abilities and uncover new methods, making this a really enriching and pleasurable interest.
Gathering Supplies: Important Instruments and Provides
Important Clay Varieties
Clay is the first materials utilized in sculpting clay folks. Various kinds of clay differ of their properties, akin to hardness, drying time, and firing temperature. Understanding the traits of every sort is essential for choosing probably the most appropriate clay to your mission:
-
Polymer clay: A pliable, oven-bake clay that doesn’t require kiln firing. It’s gentle and straightforward to mould, making it ideally suited for novices and small-scale initiatives.
-
Air-dry clay: A self-hardening clay that dries naturally and not using a kiln. It’s barely more durable than polymer clay and requires extra effort and time to work with. Nevertheless, it’s extra sturdy and could be painted or embellished after drying.
-
Stoneware clay: A high-fired clay that’s fired at excessive temperatures, leading to a dense and sturdy materials. It’s appropriate for bigger sculptures and purposeful gadgets that require energy and sturdiness.
-
Porcelain clay: A white or translucent clay that’s identified for its advantageous texture and excessive firing temperature. It’s prized for its delicate and stylish look.
Important Instruments
Along with clay, numerous instruments are important for sculpting clay folks:
- Modeling instruments: A set of instruments used for shaping and manipulating clay, together with loop instruments, scrapers, and modeling knives.
- Wire: Skinny wire used to create armatures, which give a structural framework for giant or advanced clay sculptures.
- Sponges and brushes: Used for smoothing and mixing clay surfaces.
- Rolling pin: Used for rolling out flat sheets of clay.
- Kiln: A high-temperature oven used to fireside clay items and make them sturdy. (Non-compulsory for polymer clay and air-dry clay.)
Further Provides
Different provides could improve your clay sculpting expertise:
- Glazes: Pigmented liquids used so as to add coloration and shine to fired clay items.
- Paints: Acrylic or watercolor paints used to brighten air-dry clay items.
- Sandpaper: Used for smoothing fired or dried clay surfaces.
- Apron and gloves: Protecting gear to stop stains and mess.
Including Options: Eyes, Nostril, Mouth, and Expressions
Deliver your clay folks to life by including distinctive options. Begin with the eyes. Roll out small balls of white clay and flatten them. Use a toothpick to create pupils. Black or brown clay works nicely for the pupils. As soon as the eyes are dry, dab a contact of clear glaze on them to present them a shiny look.
Subsequent, form the nostril. You need to use a small ball of clay and gently pinch it right into a triangular form. Or, you may create a extra elaborate nostril by sculpting it with a toothpick. Keep in mind, there is not any proper or unsuitable approach to do it. Let your creativeness information you.
Mouths and Expressions
The mouth is the place you may actually add character to your clay folks. Roll out a skinny strip of white clay after which fold it in half. Lower out the specified form of the mouth, akin to a smile, a pout, or a smirk. Connect the mouth to the face and use a toothpick to create any extra particulars, akin to tooth or dimples.
Expressions could be conveyed via the form of the mouth, the place of the eyes, and the lean of the pinnacle. Experiment with totally different mixtures to create a variety of feelings. This is a desk with some examples:
Expression |
Mouth Form |
Eye Place |
Head Tilt |
Pleased |
Upward curve |
Barely open |
Barely ahead |
Unhappy |
Downward curve |
Closed or teary |
Barely again |
Offended |
Straight line or frown |
Narrowed |
Barely ahead |
Stunned |
Open extensive |
Large open |
Again |
Keep in mind, the probabilities are limitless. So have enjoyable and let your creativity circulation!
Crafting Particulars: Clothes, Hair, and Equipment
Clothes
Clothes for clay folks could be constructed from numerous supplies, akin to cloth scraps, felt, and even paper. Cloth scraps can present intricate textures and patterns, whereas felt is thicker and extra sturdy. For a extra practical look, think about using doll garments or miniature tailoring methods.
Hair
Hair could be added to clay folks utilizing a wide range of methods, together with sculpting with clay or utilizing pure supplies like yarn, thread, and even actual hair strands. Sculpting hair out of clay permits for full customization of texture and elegance, however it may be time-consuming. Pure supplies supply a extra practical look however could require extra shaping and securing.
Equipment
Equipment can add character and individuality to clay folks. Think about using small beads, buttons, or sequins for jewellery and different gildings. Different gadgets, akin to hats, glasses, or scarves, could be constructed from felt or cloth scraps. For much more artistic equipment, strive sculpting mini variations of objects like musical devices or sports activities gear.
Customizing Clothes and Equipment
To personalize your clay folks’s clothes and accessories, think about using unconventional supplies or including intricate particulars. As an illustration, use scraps of lace or ribbons for female aptitude or miniature zippers and snaps for practical clothes closures. Experiment with numerous colours and textures to create distinctive and attention-grabbing outfits to your clay creations.
Materials |
Utilization |
Cloth scraps |
Clothes, particulars |
Felt |
Clothes, equipment |
Paper |
Clothes, equipment |
Yarn |
Hair |
Thread |
Hair |
Beads |
Jewellery |
Buttons |
Clothes |
Drying and Ending: Preserving Your Creation
As soon as your clay creation is full, it is important to dry and end it correctly to make sure its sturdiness and wonder.
1. Drying the Clay
Permit your creation to air dry at room temperature. The drying time will differ relying on the scale and thickness of the piece.
2. Controlling the Drying
Cowl your creation with a moist material to decelerate the drying course of and stop cracking. That is particularly vital for bigger items.
3. Avoiding Direct Daylight
Maintain your clay creation out of direct daylight, as it could possibly trigger fading or warping.
4. Hardening in an Oven
For sure kinds of clay, you may pace up the drying course of by baking it in an oven at a low temperature. Observe the producer’s directions fastidiously.
5. Ending the Floor
As soon as the clay is dry, you may apply a end to boost its look and shield it from water and dirt.
6. Acrylic Paints
Acrylic paints can be utilized so as to add coloration and element to your creation. They’re obtainable in a variety of colours and could be blended to create customized shades.
7. Sealants and Varnishes
Apply a transparent sealant or varnish to guard your creation from water and put on. This may give it a shiny or matte end.
8. Mixing Strategies
Experiment with totally different mixing methods to create distinctive textures and colours. You may combine acrylic paints, sealants, and even different supplies like glitter or sand.
9. Defending Your Creation
Retailer your clay creation in a cool, dry place. Keep away from excessive temperatures or moisture, as these can harm the end.
10. Repairing Cracks
In case your creation cracks in the course of the drying course of, you may restore it utilizing a mix of water and glue. Apply the combination to the crack and clean it out. Permit it to dry fully earlier than making use of any finishes.
How you can Make Clay Folks
Creating clay folks is a enjoyable and rewarding interest that anybody can get pleasure from. With just a little apply, you may create practical and expressive figures that may convey pleasure to your property or workplace.
Supplies
To make clay folks, you’ll need the next supplies:
- Clay
- Water
- Modeling instruments
- Paint (optionally available)
Directions
- Put together the clay. Begin by kneading the clay till it’s gentle and pliable. If the clay is just too dry, add just a little water. If the clay is just too moist, add just a little extra clay.
- Create the essential form of the determine. Use your fingers to type the essential form of the determine. You need to use the modeling instruments to refine the form and add particulars.
- Add the small print. After getting the essential form of the determine, you may add the small print. Use the modeling instruments to create the eyes, nostril, mouth, hair, and different options.
- Bake the determine. As soon as you might be glad with the determine, bake it in line with the producer’s directions. This may harden the clay and make it everlasting.
- Paint the determine (optionally available). If you’d like, you may paint the determine utilizing acrylic paints. This may add coloration and character to your creation.
Folks Additionally Ask About How you can Make Clay Folks
How lengthy does it take to make a clay particular person?
The time it takes to make a clay particular person will differ relying on the scale and complexity of the determine. A easy determine could be made in a couple of hours, whereas a extra advanced determine could take a number of days and even weeks to finish.
What sort of clay is greatest for making folks?
There are numerous various kinds of clay that can be utilized for making folks. Among the hottest varieties embrace polymer clay, air-dry clay, and water-based clay. Polymer clay is an efficient alternative for novices as a result of it’s simple to work with and doesn’t require baking. Air-dry clay is one other good possibility for novices as a result of it’s self-hardening and doesn’t require baking. Water-based clay is a extra conventional sort of clay that requires baking to harden.
How do you make clay folks look practical?
There are some things you are able to do to make your clay folks look extra practical. First, take note of the small print. The extra particulars you add, the extra practical your determine will look. Second, use practical colours. Keep away from utilizing vivid or unnatural colours. Third, bake your determine correctly. If the determine is just not baked correctly, will probably be weak and brittle.